|
|
วิธีเขียนคู่มือคำแนะนำ
Work
Instruction |
|
ลำดับที่หนึ่ง เขียนขั้นตอนงาน Work
Steps or Work Statements |
การเตรียมการเพื่อเขียนขั้นตอนงาน
เริ่มจากทำความเข้าใจขอบเขตของงานและสำรวจพื้นที่จริง
หลังจากนั้นจึงเริ่มกำหนดขั้นตอนงาน
โดยเริ่มจากกำหนดขั้นตอนหลักและนำขั้นตอนหลักมาแจกแจงเป็นขั้นตอนย่อยๆ |
ขั้นตอนหลักคือขั้นตอนที่บอกลำดับการทำงานกว้างๆ
ไม่อธิบายลงรายละเอียด
ส่วนขั้นตอนย่อยคือการนำขั้นตอนหลักมาแจกแจงลงรายละเอียดเป็นภาษากริยาว่าให้ทำอย่างไร
เช่น ถอดออก ประกอบ ขั้นกวด ตรวจสอบ ฯลฯ เป็นต้น |
กรณีศึกษาอย่างง่าย
เกี่ยวกับการเขียนขั้นตอนปฏิบัติงาน |
แผนภาพเป็นถังเก็บน้ำหล่อเย็นอุปกรณ์เตาหลอมซิลิกาของโรงงานผลิตกระจก
ซึ่งในภาวะเดินเครื่องปกติอุณหภูมิของเตาจะสูงประมาณ ๑๔๐๐ ถึง ๑๕๐๐ องศาเซนเซียส
กรณีไฟฟ้าดับต้องมีน้ำหล่อเย็นปล่อยลงมาจากด้านบนเพื่อค่อยๆ
ลดอุณหภูมิของอุปกรณ์ป้อนทรายแก้ว ป้องกันไม่ให้อุปกรณ์เสียหาย
จึงติดตั้งถังน้ำไว้สองระดับ (ดังภาพ)
ไว้บนเพลทฟอร์มถาวรด้านบนอุปกรณ์ของเตา |
สถานการณ์สมมุติ
:
ปะเก็นของวาล์วด้านจ่ายรั่ว
มีคำสั่งงานเปลี่ยนปะเก็น |
|
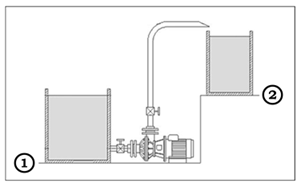
|
|
|
ประเด็นพิจารณาหลังทำสำรวจพื้นที่
ประเด็นแรก-แม้ถังน้ำหล่อเย็นจะอยู่ที่สูงแต่ติดตั้งบนเพลทฟอร์มถาวร
คนทำงานเดินขึ้นลงทางบันไดโดยไม่ต้องใช้อุปกรณ์อื่นมาติดตั้งเพิ่มอีก
ประเด็นที่สอง-อุปกรณ์ที่ต้องเปลี่ยนเป็นปะเก็นซึ่งน้ำหนักเบาและใช้เครื่องมือช่างขั้นพื้นฐานเท่านั้น
ไม่ต้องมีจักรกลผ่อนแรงเพื่อขนย้าย
ดังนั้นจึงเขียนขั้นตอนปฏิบัติเหมือนกับทำงานที่ระดับพื้นล่าง | |
| |
ต้องเปลี่ยนปะเก็นวาล์วด้านจ่าย
จึงกำหนดการปฏิบัติงานเป็นสี่ขั้นตอนหลัก | |
- การเตรียมการ ตัดแยกพลังงานและล็อคเอาท์ระบบ
- ถอดวาล์วด้านจ่ายเพื่อเปลี่ยนปะเก็น
- เปลี่ยนปะเก็นและประกอบชิ้นส่วนของปั๊มกลับเช่นเดิม
- ตรวจสอบความเรียบร้อยของงานและทดลองเดินเครื่อง
| |
จะเห็นได้ว่าขั้นตอนหลัก
มีเจตนารมณ์เพียงบอกลำดับปฏิบัติเป็นกลุ่มงานเท่านั้น
ส่วนรายละเอียดว่าให้ทำอย่างไรก่อนหลังยังไม่มี จึงนำไปสนับสนุนการทำงานไม่ได้
ดังนั้นจึงต้องนำแต่ละขั้นตอนหลักไปแจกแจงเป็นขั้นตอนย่อย |
|
|
|
ลำดับที่สอง ชี้บ่งและระบุอันตราย Hazards
Identified |
|
ลำดับทีสอง
ให้นำทุกขั้นตอนย่อยมาชี้บ่งและระบุอันตราย
โดยชี้บ่งอันตรายให้ครอบคลุมทั้งสี่กลุ่ม ตัวอย่างเช่นนำขั้นตอนที่
๒.๑
มาชี้บ่งอันตราย ก็ให้ดูว่าในขั้นตอนนี้มีอันตรายทางกายภาพ เคมี
ชีวภาพและเออร์กอนโอมิกส์หรือไม่
สมมุติว่ามีอันตรายทางด้านกายภาพ ก็ต้องระบุว่าเป็นอันตรายลักษณะใด สั่นสะเทือน
หรือบาด หรือตัด หนีบ ทิ่มแทง ฝุ่นควัน ร้อนหนาว กระแทกชน ฯลฯ
ต้องระบุว่ามีอันตรายลักษณะใด |
การชี้บ่งและระบุอันตรายนั้น
ต้องทำเป็นลำดับขั้นและต้องครอบคลุมอันตรายทุกกลุ่มทั้งอันตรายทางด้านกายภาพ เคมี
ชีวภาพและเออร์กอนโอมิกส์ เพื่อให้เข้าใจโดยง่าย
จึงสรุปขั้นตอนการชี้บ่งและระบุอันตรายดังนี้ |
|
|
|
ลำดับที่สาม กำหนดมาตรการควบคุมอันตราย Control
Measure |
|
มาตรการควบคุมอันตรายตามทฤษฎีคือ
ควบคุมที่แหล่งกำเนิด ความคุมที่ทางผ่านและควบคุมที่ตัวคนทำงาน (source,
patch and receiver) ณ ที่นี้ไม่ได้บอกว่าผิด
แต่นำมาใช้งานยากเนื่องจากขอบเขตกว้างเกินไป
ในแง่ประยุกต์ใช้จึงแนะนำให้เลือกวิธีควบคุมอันตรายเป็นลำดับขั้น (hierarchy
of control) จะง่ายกว่าและควบคุมอุบัติเหตุได้มีประสิทธิภาพสูงกว่า |
|
การควบคุมอุบัติเหตุเป็นลำดับขั้น
Hierarchy
of Control |
|
- แยกงานออกจากอันตราย
eliminate
get rid of the hazard : แม้หลักการควบคุมอุบัติเหตุได้กล่าวถึงเรื่องนี้ไว้อย่างละเอียด
ทว่าการแยกอันตรายออกจากงาน นำมาใช้งานจริงในแง่งานปฏิบัติการซ่อม สร้าง
กู้สภาพยากลำบาก ในที่นี้จึงไม่กล่าวถึงโดยละเอียด
แต่จะแนะนำให้ควบคุมอันตรายโดยใช้มาตรการ ๒-๔
มากกว่าซึ่งมาตรการ ๒-๔
สำหรับควบคุมอุบัติเหตุ จะกล่าวถึงในลำดับต่อจากนี้
- ใช้วิธีหรือกระบวนการที่อันตรายน้อยกว่าแทน
substitute replace
with
less
hazardous
material
or
process : สำหรับกระบวนการคิดในการควบคุมอุบัติเหตุต้องพยายามมองถึงหลายๆ
ตัวเลือก เงื่อนไขใดอันตรายน้อยกว่าและประสิทธิภาพงานเท่าเดิม
ให้เลือกเงื่อนไขนั้นแทน ตัวอย่างเช่น
กระบวนการทำงานใช้บันไดพาดเพื่อขึ้นลงทำงานบนที่สูง
ปรับเครื่องมือใหม่เปลี่ยนจากบันไดพาดมาใช้นั่งร้านหรือใช้รถกระเช้าแทน
|
บางขั้นตอนของงานระบุให้ขนย้ายของด้วยรถยก แต่เมื่อพิจารณาลงในรายละเอียดพบว่าของที่จะขนยายนำหนักประมาณ ๑๕-๒๐ กิโลกรัม ขนย้ายเพียงระยะทางสั้นๆ และเป็นงานลักษณะที่ทำเป็นครั้งคราว (one off job or infrequent job) จึงเลือกใช้ hand pallet truck แทนรถยก ติดตั้งนั่งร้านท่อประกอบเพื่อใช้ในงานซึ่งมีความร้อนและประกายไฟ จึงระบุให้ใช้พื้นนั่งร้านแบบโลหะแทนการใช้พื้นนั่งร้านที่เป็นไม้ ฯลฯ เป็นต้น |
|
- เครื่องป้องกันระหว่างอันตรายกับคนหรือตัดแยกระบบ
engineering
a solution (barriers, isolation)
guards between people and hazards : คือการใช้อุปกรณ์ฮาร์ดแวร์เพื่อควบคุมอันตราย
ซึ่งเรามักเรียนรู้เป็นสามกลุ่ม กลุ่มแรกเป็นแถบกันเตือน แถบกั้นอันตรายและธงริ้ว,
รั้วแข็ง
สัญลักษณ์ความปลอดภัยและหมายความรวมถึงการนำมาใช้หรือยกเลิกอุปกรณ์ฮาร์ดแวร์ตามลักษณะงานด้วย
ตัวอย่างเช่น
|
- ตัดแยกพลังงานให้ครบคลุมอุปกรณ์ทางไฟฟ้า
อุปกรณ์ทางกล พลังงานสะสมจากของที่วางสูงจากพื้น (stored
energy) และล็อคเอาท์ระบบก่อนซ่อม
สร้าง กู้สภาพหรือแปลงสภาพเครื่องจักรโรงงาน
- ขีดสีตีเส้นเหลืองดำ
ขึงล้อมด้วยแถบเหลืองดำ ขึงล้อมด้วยธงริ้วเหลืองดำหรือใช้ไฟวับวาบสีเหลือง
แสดงเขตเตือนให้ระวังอันตราย
- ขีดสีตีเส้นขาวแดง
ขึงล้อมด้วยแถบขาวแดง ขึงล้อมด้วยธงริ้วขาวแดงหรือใช้ไฟวับวาบสีแดง
แสดงเขตอันตรายห้ามเข้า
- ทำงานสูงจากพื้น
ติดตั้งตาข่ายป้องกันของตกไม่ให้ของที่ตกโดนคนที่ทำงานอยู่ด้านล่าง
- เขตก่อสร้างติดตั้งรั้วแข็งแรงสูงสองเมตรและติดตั้งป้ายพื้นขาวตัวหนังสือสีแดง
ข้อความเขตก่อสร้างห้ามเข้า
- ทำงานใกล้เส้นทางสัญจรวางกรวยจราจรเป็นช่วงๆ
ก่อนถึงพื้นที่ทำงานและในระยะห้าเมตรกับพื้นที่ทำงานวางผนังปูนความสูงเก้าสิบเซนติเมตร
ที่ผนังปูนมีสีสะท้อนแสงเป็นแถบเฉียงสลับสีขาวแดง
- พื้นที่ซึ่งจะเข้าไปซ่อมบำรุงเครื่องจักรคับแคบ
จึงถอดท่อที่กีดขวางออกเป็นการชั่วคราว หลังงานแล้วเสร็จจะประกอบกลับที่เดิม
- งานซ่อมบำรุงเครื่องจักรบนเพลทฟอร์มสูงสี่เมตร
ชิ้นส่วนที่ถูกถอดออกขณะซ่อมบำรุงใช้วิธียึดรั้งไม่ให้ตกลงด้านล่าง
- ติดตั้งสัญญาณแสงและสัญญาณเสียง
เมื่อจักรกลขนถ่ายทำงาน ฯลฯ
|
|
- กำหนดนโยบาย
มีระบบเอกสารสนับสนุนการปฏิบัติงาน
เช่นขออนุญาตทำงาน ระเบียบปฏิบัติ คู่มือคำแนะนำ ใช้มาตรฐานสากล ใช้กฎหมาย
ฝึกอบรมคน ฯลฯ เป็นต้น
- ใช้อุปกรณ์คุ้มครองความปลอดภัยส่วนบุคคล
ตรงกับลักษณะงาน อุปกรณ์คุ้มครองความปลอดภัยส่วนบุคคลแบ่งออกเป็นสองกลุ่มคือ
อุปกรณ์ระดับพื้นฐานและระดับพิเศษเฉพาะงาน
|
การควบคุมอุบัติเหตุให้ใช้อุปกรณ์คุ้มครองความปลอดภัยส่วนบุคคล
เป็นมาตรการร่วมเท่านั้น หมายถึงนอกจากจะใช้มาตรการข้างต้นแล้วก็ให้ใช้
อุปกรณ์คุ้มครองความปลอดภัยส่วนบุคคลร่วมด้วย |
|
การขออนุญาตทำงาน Permit to Work or Work Permit |
|
การขออนุญาตทำงานถือว่าเป็นรากฐานสำคัญและมีความจำเป็นต้องจัดทำอย่างมีคุณภาพ
รายละเอียดของเอกสารจะกำหนดขอบเขตของการทำงาน ขั้นตอนหลัก ขั้นตอนย่อย
ชี้บ่งระบุอันตรายและควบคุมอันตรายในทุกขั้นตอนของกระบวนการทำงาน
จริงแล้วระบบนี้ถูกนำมาใช้และพัฒนาต่อเนื่องมาแต่แต่ช่วงปี ๒๕๓๐
กระทั่งวันนี้นับว่านานพอควร ทว่าประเทศไทยและภาคพื้นใกล้เคียงกลับคืบเดินช้า
ถูกนำมาใช้เพียงเล็กน้อยเท่านั้น
หากประเมินโดยหยาบประสิทธิภาพไม่เกินสี่สิบเปอร์เซ็นต์
เอกสารฉบับนี้จะเป็นส่วนหนึ่งในการพัฒนาระบบขออนุญาตทำงาน |
|
อธิบายเจ็ดขั้นตอนการเปิดงาน |
ขั้นตอนที่หนึ่ง
ระบุขอบเขตและรายละเอียดของงานที่จะปฏิบัติ
Job Detail : หมายถึงให้ระบุชื่องานที่จะทำและรายละเอียดที่เกี่ยวข้อง
ซึ่งแต่ละองค์กรอาจกำหนดแบบฟอร์มแตกต่างกันบ้าง
แต่ขั้นต่ำต้องมีรายละเอียดดังต่อไปนี้ |
|
- ชื่องาน
job
title เขียนระบุชื่องานในแบบฟอร์มว่าจะทำอะไร
ตัวอย่างเช่น งานติดตั้งรางสายไฟผนังคลังสินค้า ๔ ที่ระดับสูงแปดเมตร
เปลี่ยนปะเก็นวาล์วด้านดูดปั้มส่งน้ำดิบที่เพลทฟอร์มชั้นสองของแทงค์ฟาร์ม
ซ่อมเพลาขับสายพานลำเลียงของเครื่องบรรจุภัณฑ์ ฯลฯ เป็นต้น
- หมายเลขงาน
job
id number หมายเลขงานให้กำหนดขึ้นเอง
ใช้เฉพาะการหยุดซ่อมบำรุงตามแผนและการซ่อมบำรุงในคราวนั้นมีจำนวนงานเกินสามงาน
เหตุผลคือจะทำให้การบริหารงานซ่อมบำรุงง่ายขึ้น
ส่วนกรณีที่ซ่อมเครื่องจักรขัดข้องในลักษณะ
break
down maintenance จะกำหนดหรือไม่กำหนดหมายเลขงานก็ได้ (optional
not mandatory)
- พื้นที่ปฏิบัติงาน
working
area ให้ระบุว่าทำงานที่ส่วนงานใดหรือพื้นที่ใด
ตัวอย่างเช่น ส่วนงานขึ้นรูปท่อเหล็ก โรงบำบัดน้ำเสีย
ฯลฯ
- ชื่อเครื่องจักรหรือชื่ออุปกรณ์
equipment
หมายถึงให้เขียนบันทึกลงในแบบฟอร์มว่าเครื่องจักรหรืออุปกรณ์ที่จะเข้าไปทำงานชื่ออะไร
- วันเริ่มงานและกำหนดเสร็จ
start
date-finish date การขออนุญาตทำงานต้องมีแผนทำงาน
ในที่นี้จึงหมายถึงเวลาตามแผนและหากว่าระยะเวลาปฏิบัติงานจริงยาวกว่าที่แผนกำหนดไว้
ให้ประสานเจ้าของหน่วยงานเพื่อขออนุญาตขยายเวลาทำงาน
|
|
ขั้นตอนที่สอง
เอกสารแนบเพื่อขออนุญาตทำงาน
Permit
to Work Elements เอกสารแนบเพื่อขออนุญาตทำงานมีสองส่วนคือ |
- เอกสารคู่มือคำแนะนำหมายถึงเอกสารที่มีสามองค์ประกอบคือ
หนึ่งขั้นตอนปฏิบัติงาน work steps สองชี้บ่งระบุอันตรายงานแต่ละขั้นตอน
hazard
identified และสามขั้นตอนใดที่ชี้บ่งและถูกระบุว่าอาจเกิดอันตรายให้กำหนดมาตรการควบคุมป้องกัน
control
measure
- ใบรายการตัดแยกพลังงานและล็อค-เอาท์ระบบ
(energy
isolation and lockout list) ซึ่งหมายถึงเอกสารซึ่งแสดงรายการว่าต้องตัดแยกพลังงานใดบ้างและตัดแยกที่อุปกรณ์ใดเช่น
เบรกเกอร์ทางไฟฟ้า วาล์วทางกล
|
|
ขั้นตอนที่สาม ยื่นเอกสารขออนุญาตทำงานกับเจ้าของหน่วยงาน
Permit
to Work เจ้าของหน่วยงานหรือเจ้าของพื้นที่ |
เจ้าของหน่วยงานหรือเจ้าของพื้นที่
หมายถึงพนักงานบังคับบัญชาระดับต้น (front
line leader) ประจำพื้นที่นั้นซึ่งผู้อนุญาตดังกล่าวนี้ต้องผ่านการฝึกอบรม
(qualified
person) ไม่เช่นนั้นกระบวนการ
permit
to work ก็จะขาดคุณภาพ
เนื่องจากเอกสารอาจลงนามโดยผู้ที่ขาดความรู้ ความสามารถ |
เอกสารที่หัวหน้ากลุ่มงาน
job
leader ต้องยื่นขออนุญาตทำงานมีทั้งหมดสามฉบับคือ
หนึ่งใบขออนุญาตทำงาน permit to work ซึ่งถือว่าเป็นใบหลัก
สองคู่มือคำแนะนำหรือใบตรวจสอบ
work
instruction or checklist และสามใบรายการตัดแยกพลังงานและล็อค-เอาท์ระบบ
(ถ้ามีการตัดแยกพลังงาน) |
|
เจ้าของหน่วยงานหรือเจ้าของพื้นที่
area
owner จะพิจารณาจากสองเงื่อนไข
ก่อนลงนามอนุญาต |
|
- เอกสารที่ยื่นขออนุญาตทำงานครบหรือไม่
- หากครบ
เอกสารได้คุณภาพหรือไม่
|
หากเอกสารครบและได้คุณภาพเจ้าของหน่วยงานก็จะลงนามอนุญาต
หากว่ามีข้อแนะนำเกี่ยวกับมาตรการป้องกันควบคุมอุบัติเหตุที่สำคัญๆ
ก็สามารถเขียนให้คำแนะนำลงในลำดับนี้ได้ hazards
identified and additional control methods by area owner |
|
ขั้นตอนที่สี่
หัวหน้ากลุ่มงาน
Job
Leader ลงนามในใบขออนุญาตทำงานเพื่อแสดงว่ารับทราบว่าถูกอนุญาตให้ทำงานในขอบเขต
ตามที่ระบุในเอกสารได้ ขั้นตอนที่ห้า
หัวหน้ากลุ่มงาน
Job
Leader ประสานช่างเทคนิคประจำพื้นที่เพื่อตัดแยกพลังงานและล็อค-เอาท์ระบบ
และต้องไม่ลืมว่าการทำงานในลำดับนี้ต้องมีขั้นตอนที่ชัดเจนและแม่นยำ |
|
- ประสานช่างเทคนิคประจำพื้นที่เพื่อทำสำรวจจุดตัดแยกพลังงานและทำสำรวจการปิดกั้นควบคุมพื้นที่ปฏิบัติงาน
- หัวหน้ากลุ่มงานร่วมกับช่างเทคนิคประจำพื้นที่
(job
leader-authorized isolator) ร่วมกันจัดทำใบรายการตัดแยกพลังงานและล็อค-เอาท์ระบบ
- นำใบรายการตัดแยกพลังงานและตัดแยกระบบไปที่หน้างาน
ช่างเทคนิคตัดแยกพลังงานและหัวหน้ากลุ่มงานล็อคอุปกรณ์ตัดแยกพลังงานด้วยกุญแจสี equipment
padlock
- ร่วมทดสอบว่าระบบตาย
หากระบบตายก็สามารถทำงานขั้นตอนต่อไปได้ ในทางตรงข้ามหากระบบไม่ตายให้หยุดการทำงาน
หัวหน้ากลุ่มงานเขียนใบรายงานอุบัติการณ์
incident
investigation report และการตัดสินใจหลังจากรายงานอุบัติการณ์
ให้อยู่ในดุลพินิจของผู้จัดการต้นสังกัด
- ปิดกั้นควบคุมพื้นที่ปฏิบัติงาน
|
ขั้นตอนที่หก
ประชุมกลุ่มก่อนเริ่มงาน
๕-๑๐
นาที Crew
Briefed or Tool Box Meeting) หัวหน้ากลุ่มงานเป็นผู้นำการประชุม
ซึ่งการพูดคุยจะแบ่งเป็นสามส่วนคือ หนึ่งสรุปขอบเขตและขั้นตอนหลักๆ ของงานที่จะทำ
สองอันตรายที่อาจเกิดและสามมาตรการควบคุมอันตราย
ต้องไม่ลืมว่าการประชุมต้องให้ทีมมีส่วนร่วมแสดงความคิดเห็น เสนอแนะหรือสอบถามได้ ขั้นตอนที่เจ็ด
ผู้ปฏิบัติงานลงชื่อเข้าทำงานและแขวนกุญแจส่วนบุคล
Personal
Padlock ที่สถานีควบคุมการทำงาน |
|
|
|
บอร์ดควบคุมสถานีการทำงาน |
|
ลักษณะบอร์ดสถานีควบคุมการทำงาน
หมายเลขหนึ่ง คลิ๊บใบขออนุญาตทำงานและคู่มือคำแนะนำ
หมายเลขสอง
คลิ๊บใบรายการตัดแยกพลังงานและล็อค-เอาท์ระบบ
หมายเลขสาม
กล่องโปร่งใสทรงสี่เหลี่ยมแบนสำหรับเก็บลูกกุญแจ equipment
padlock และหมายเลขสี่คือเหล็กบาร์สำหรับล็อคกล่องซึ่งจะถูกล็อคด้วยกุญแจสีสองชนิดคือ |
- กุญแจสีหัวหน้ากลุ่มงาน
สีเขียว job
leader padlock
- กุญแจสีผู้ปฏิบัติงาน
สีแดง personal
padlock
|
|
การใช้บอร์ดควบคุมสถานีการทำงาน |
|
ลำดับที่หนึ่ง หลังจากตัดแยกพลังงานและล็อคเอาท์ระบบเรียบร้อยแล้ว
หัวหน้ากลุ่มงาน job leader นำใบขออนุญาตทำงานและเอกสารคู่มือคำแนะนำคลิ๊บไว้ที่
หมายเลขหนึ่ง (ดูแบบฟอร์มใบขออนุญาตทำงานประกอบการอ่าน)
ใบรายการตัดแยกพลังงานและล็อค-เอาท์ระบบคลิ๊บไว้ที่หมายเลขสอง
และนำลูกกุญแจสี equipment padlock มาไว้ในกล่องหมายเลขสาม ลำดับที่สอง กล่องหมายเลขสาม
ที่บาร์ล็อคกุญแจสีหมายเลขสี่ หัวหน้ากลุ่มงานล็อคกุญแจสี job
leader padlock และผู้ปฏิบัติงานล็อคกุญแจสี personal
padlock ของตัวเอง
ซึ่งการทำดังกล่าวนี้
ลูกกุญแจ equipment
padlock ซึ่งอยู่ในกล่องไม่สามารถนำออกมาได้
เมื่อลูกกุญแจฯ นำออกมาไม่ได้ก็ไม่สามารถเปิดคืนระบบของเครื่องจักรที่ล็อคไว้ได้
จะคงสภาพให้เครื่องจักรตาย จนกว่าผู้ปฏิบัติงานจะทำงานแล้วเสร็จ ลำดับที่สาม หลังจากผู้ปฏิบัติงานแขวนและล็อคกุญแจสีของตนเองแล้วเสร็จ
ก็ให้ลงชื่อเข้าทำงานในขั้นตอนที่เจ็ดของแบบฟอร์มขออนุญาตทำงานและนับจากนี้ถือว่าเป็นการเปิดงาน
สามารถเข้าทำงานในขอบเขตที่ขออนุญาตไว้ได้ |
|
|
|
(อ่านต่อ ๖.๒ คลิ๊กตรงนี้ หรือคลิ๊กตามลิงค์ด้านล่าง) |